PROCESS
Micron precision and high-quality product processing
Quality assurance at every level of the production process
Hearing the voice of our clients is the most important step in our production process. As for the processing itself, we direct our accumulated skills for each and every product.
In addition, our high-quality results are proven by the final inspection of high-precision testers.
Our attention to quality at every level of production earned us the ISO9001 quality system certification in 2002.
Tooth-cutting/grinding and other single process orders are evidence of the trust that we have earned with our clients.
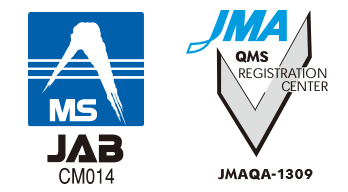
-
From initial inquiry to contract
A contract is finalized only after undergoing the steps of “Query”, “Technology & Design Discussion” and “Estimate”. An agreement is made only after all steps have been concluded to a client’s satisfactions.
For details, please see our Order Guide.
order guide -
Pre-processing for gear cutting
Process up until tooth-cutting the materials.
Approximately Φ10~Φ1200 can be handled in-house. Should other sizes be required, they can be provided with the cooperation of other factories.
-
Gear cutting
The gear cutting process. 20 gear cutters are capable of handling under Φ10 and up to Φ1900 for gears that include external tooth, internal tooth, worm screw and worm wheel.
-
Tempering / heat treatment
Cooperative factories help us meet carburizing, high frequency, nitriding and other needs of our clients.
-
Pre-processing for grinding
Precision is improved following heat treatment by finishing the products with lathe processing, milling, key processing and drilling.
-
Grinding
Grinding of inner diameter, outer diameter and end surfaces are conducted.
Vertical multitasking grinder simultaneously processes inner diameter, outer diameter and end surfaces to allow high-precision processing of concentricity and perpendicularity.
-
Gear grinding
Gear grinding process allows the output of high-precision gears that will fully satisfy a designer’s needs.
External tooth, internal tooth, worm, ball screw, screw rotor and other optional tooth profile shape gears produced according to a client’s diverse needs.
-
Inspection shipment
Highly precise gear production requires a high precision gear measurement testing. We offer micron precision measurement.
HIGH PRECISION TESTER
FACILITIES
-
Lathe machine9UnitMax Φ700 x 2000
-
Turning center1UnitMax Φ1300 x 400
-
Milling machine3Unit1000 x 300 x 500
-
Machining center2Unit1100 x 700 x 500
-
Hobbing machine15UnitMax M30 x Φ1900 x 1000
-
Gear grinding machine8UnitExternal gear grinding Max M30 x Φ1900 x 1000
Internal gear grinding Min M0.5 x Φ50 x 200
Worm screw grinding Max M30 x Φ500 x 1200 -
Worm grinding machine3UnitMax Φ250 x 2000
-
Horizontal gear cutting machine3UnitMax M10 x Φ400 x 3000
-
Grinding machine2UnitAxis grinding Φ300 x 900
Vertical type grinding Outer diameter Max Φ800 x 500
Inner diameter (Φ45)~Φ800 x 300 -
Shaper2UnitMax M6.6 Φ700 x 170
-
Keyseater machine2UnitMax 50W x Φ400 x 400
-
Rack milling machine1UnitMax M12 Φ1500
-
Radial drilling machine2UnitMAX Piercing ability Φ42
Piercing ability M25 -
Gear tester2UnitMax M30 Φ1200 x 800 Makes it possible to measure tooth profile gears at random
-
Worm wheel gear rolling tester2UnitMax Φ2250